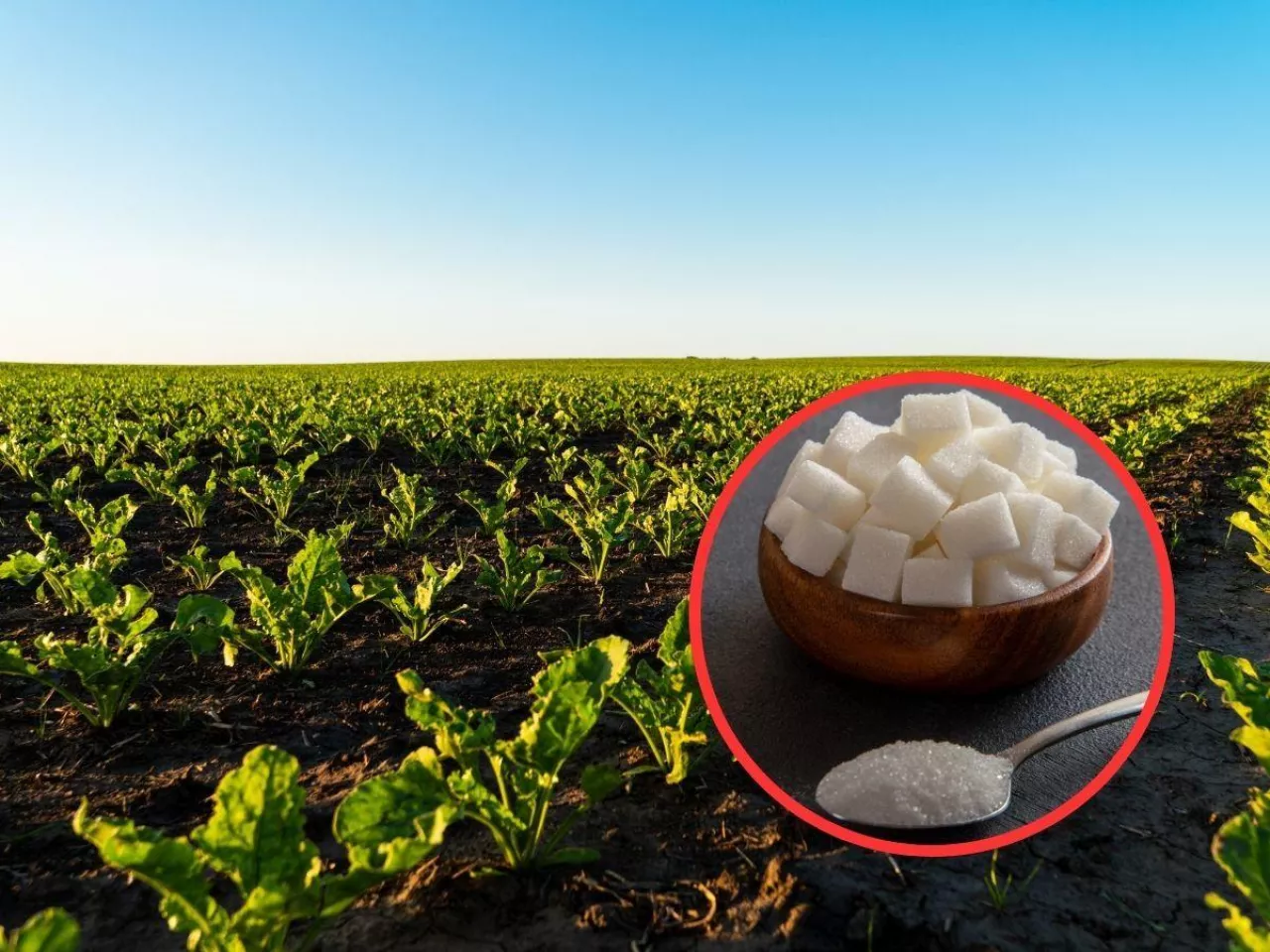
Jak modernizacja sprężarkowni i dobór odpowiednich rurociągów wpłynęły na jakość sprężonego powietrza?
Dzięki starannie dobranym średnicom przewodów, unowocześnieniu samej kompresorowni oraz zamontowaniu wysokiej klasy osuszacza sprężonego powietrza typu adsorpcyjnego udało się uzyskać wydajne i wolne od wilgoci sprężone powietrze – kluczowy czynnik wpływający na niezawodne działanie nowo powstałych obiektów.
W niniejszym Studium Przypadku szczegółowo przedstawiam zrealizowane etapy projektu oraz najważniejsze zalety wdrożonego rozwiązania, dzięki któremu cukrownia osiągnęła wyższy poziom bezpieczeństwa i efektywności produkcji.
Jak zapewnić efektywność i bezpieczeństwo sprężonego powietrza?
Przygotowanie odpowiednio zaprojektowanej infrastruktury pneumatycznej stanowi wymagające wyzwanie, które obejmuje liczne zagadnienia dotyczące wydajności, optymalizacji kosztów oraz bezpieczeństwa. Dlatego warto powierzyć to zadanie doświadczonym inżynierom, którzy dostosują rozwiązania do indywidualnych warunków danego zakładu. Zapoznaj się z owym Studium Przypadku, w którym opisano proces modernizacji sieci sprężonego powietrza w cukrowni zrealizowany przez zespół Pneumat.
Nowa sieć sprężonego powietrza i modernizacja sprężarkowni w rozbudowywanej cukrowni – wstęp do Studium Przypadku
Zgłosił się do nas inwestor, który potrzebował kompleksowego projektu, jakim jest nowa instalacja sprężonego powietrza oraz modernizacja dotychczasowej kompresorowni. Obiekt cukrowni jest rozbudowywany o kolejne sekcje: dyfuzor wieżowy, warnik oraz wymienniki, co oznacza konieczność zapewnienia im czystego i suchego sprężonego powietrza – wolnego od kondensatu i zanieczyszczeń.
Aktualny stan:
- Istniejące sprężarki powietrza w cukrowni (dwie jednostki) są wystarczająco wydajne, by sprostać zapotrzebowaniu na sprężone powietrze. Nie jest więc konieczna ich wymiana ani instalacja dodatkowego urządzenia.
- Dotychczasowa sprężarkownia nie spełnia jednak wymagań nowej infrastruktury. Trzeba ją unowocześnić, by zapewnić odpowiednie parametry medium we wszystkich nowo budowanych obiektach.
W ramach prezentowanego Studium Przypadku pokażemy, w jaki sposób opracowaliśmy rozwiązanie dostosowane do specyfiki cukrowni, gwarantując najwyższą jakość sprężonego powietrza oraz optymalną wydajność całego systemu.
Modernizacja etapu projektowego – jak usprawniliśmy proces?
W pierwszej kolejności przeprowadziliśmy dogłębny wywiad z zespołem cukrowni, aby poznać dokładne oczekiwania oraz uwarunkowania techniczne. Na tej podstawie powstał szczegółowy projekt obejmujący nową instalację sprężonego powietrza dla planowanego dyfuzora wieżowego, warnika i wymienników. W celu zapewnienia optymalnej pracy całego systemu dobraliśmy odpowiednie rury pneumatyczne: średnice – fi110 w obrębie sprężarkowni oraz fi25 w rozprowadzeniach.
Klucz do czystego powietrza – modernizacja centralnego uzdatniania
Kolejnym istotnym elementem projektu stała się unowocześniona infrastruktura w kompresorowni, ponieważ nowe obiekty wymagały sprężonego powietrza wolnego od wilgoci i zanieczyszczeń. W tym celu skupiliśmy się głównie na wymianie systemu centralnego uzdatniania powietrza. Najważniejszą częścią opracowanego rozwiązania został osuszacz adsorpcyjny regenerowany na zimno – HL 1700, który uzyskuje ciśnieniowy punkt rosy na poziomie -40°C, zapewniając sprężone powietrze o wysokiej czystości.
Urządzenie dobrano do łącznej wydajności dwóch już istniejących w sprężarkowni sprężarek powietrza (około 32,2 m³/min). Dzięki temu możliwe stało się pełne zabezpieczenie całej instalacji przed kondensatem, co spełniało wymagania stawiane przez nowo powstające obiekty w cukrowni.
Osuszacz sprężonego powietrza w kompresorowni modernizowanej cukierni
Pierwszy etap uzdatniania – ochrona osuszacza poprzez zbiornik „mokry” i filtrację
W celu zwiększenia efektywności działania osuszacza adsorpcyjnego zaprojektowaliśmy wstępny układ składający się ze zbiornika „mokrego” o pojemności 5000 L, elementu jakim był separator cyklonowy oraz filtra wstępnego 1 μm. Rozmieszczenie tych elementów tuż za kompresorami, a przed samym osuszaczem, pozwala na wstępne usunięcie skroplin, jakim jest kondensat i różnorodnych zanieczyszczeń. W rezultacie odciąża to osuszacz adsorpcyjny, który dzięki temu pracuje skuteczniej i zapewnia wyższą jakość sprężonego powietrza.
Zwiększenie czystości powietrza i stabilności ciśnienia – filtr pyłowy oraz zbiorniki buforowe
Po wyjściu z osuszacza adsorpcyjnego zaplanowaliśmy montaż filtra pyłowego (0,01 μm) oraz „suchego” zbiornika buforowego o pojemności 5000 L, który stabilizuje przepływ sprężonego powietrza w całej instalacji. Kluczowe okazało się zapewnienie niezawodnego dostarczania medium na sam szczyt wieży dyfuzora, gdzie punkt odbioru znajduje się na wysokości ok. 50 m. Aby zagwarantować bezpieczny i ciągły transport sprężonego powietrza na taką wysokość, umieściliśmy przy podstawie dyfuzora dodatkowy, bocznikowo podłączony zbiornik o pojemności 300 L, który pełni rolę lokalnego buforu.
Od lewej: zewnętrzny zbiornik ciśnieniowy typu suchego, na prawo zbiornik o pojemności 300 litrów umiejscowiony pośrodku dyfuzora na samym dole
Dostosowanie rozwiązań i optymalizacja kosztów – efektywna sieć zasilania w sprężone powietrze
Zastosowane w projekcie innowacje zostały ściśle dopasowane do wymagań zamawiającego oraz istniejącej w cukrowni infrastruktury. W efekcie udało się ograniczyć koszty, jednocześnie zapewniając instalacji wydajność idealnie dostosowaną do potrzeb zakładu. Zarówno kompletna sieć, jak i sprężarkownia zostały zaplanowane tak, aby zaopatrywać wszystkie układy w odpowiednią ilość właściwie uzdatnionego powietrza. Uzyskane rozwiązanie jest wysoce wydajne, sprzyja racjonalnemu wykorzystaniu energii i dba o bezpieczeństwo pracowników.
Szukasz specjalistycznego wsparcia w obszarze projektowania i modernizacji instalacji sprężonego powietrza?
Skontaktuj się z działem DRI firmy Pneumat System – zespół ekspertów z wieloletnim doświadczeniem w obsłudze zakładów z różnych sektorów przemysłu zagwarantuje indywidualne i efektywne rozwiązania dopasowane do Twoich potrzeb.